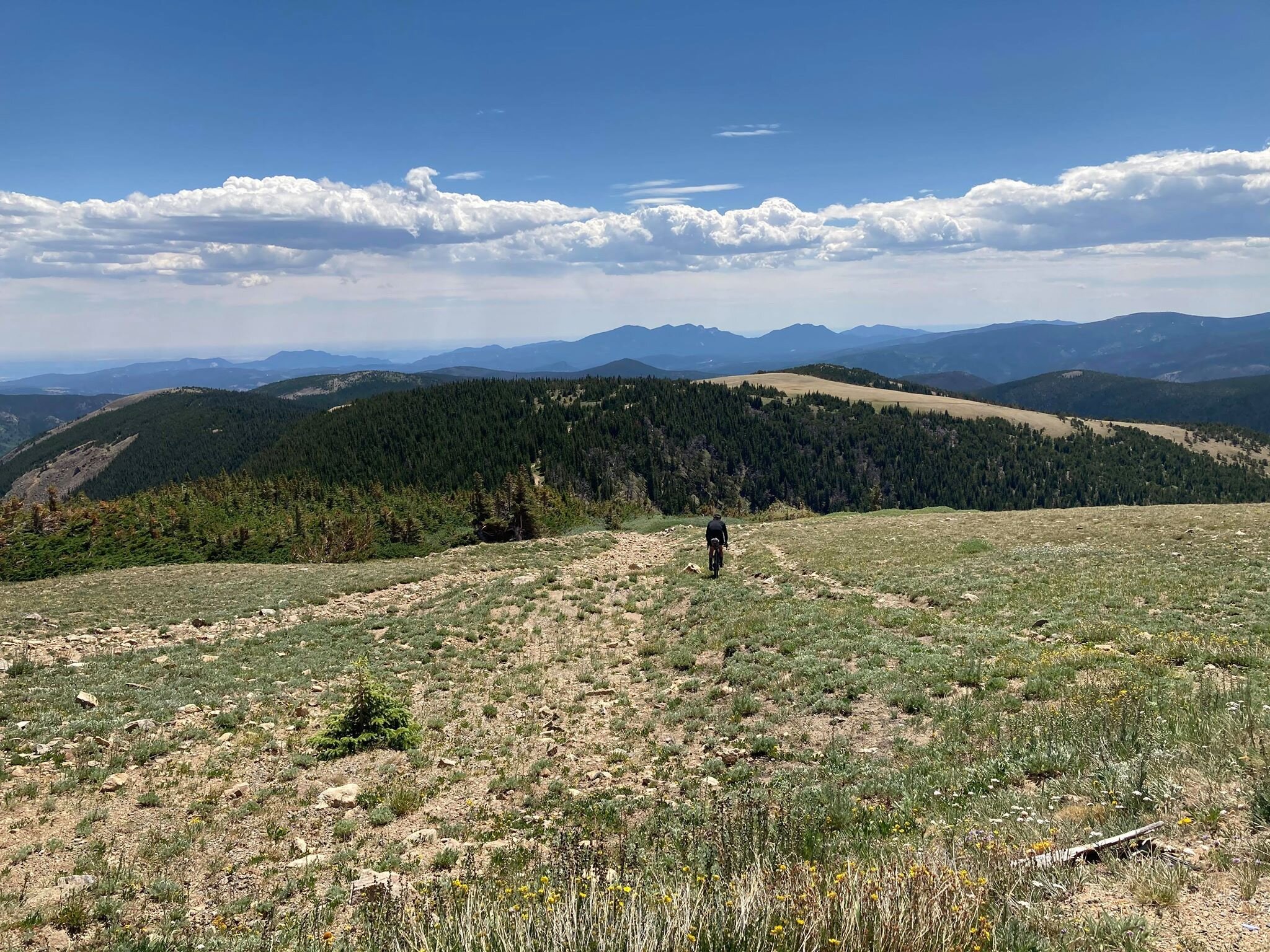
Inspirations
Explore the elevated life in the mountains. This content debuted in 2015 with Alpine Modern’s printed quarterly magazine project.
Minimalist Pottery in the Kyoto Mountains
An intimate visit with husband-and-wife pottery artists Momoko and Tetsuya Otani at their home and studio in Japan
The Shinkansen bullet train from Tokyo to Kyoto departs not one minute late, travels almost 200 miles an hour, passes Mount Fuji on the way, and pulls into Kyoto’s vaulting modern station not one minute early. From there it’s 40 kilometers by car to Shigaraki, an industrial mountain town, where I’ve come to visit a ceramic artist whose work has transfixed me on Instagram for the past ten months.
Shigaraki is home to one of Japan’s “six old kilns.” The most admired pottery here—tea bowls and sake cups made from local iron-rich clay—is often misshapen and haphazardly glazed. Much is left to the felicitous violence of earth and fire in wood-fueled kilns. These clay items, used in the exquisitely calibrated tea ceremony, are prized for their imperfections, reflecting the wabi-sabi philosophy in which earthiness, transience, roughness and decay reveal the essential nature of the world.
Such is Japan: hyper-curated, thrillingly modern, clockwork precise—then offering you a tea bowl that seems primeval.
The ceramic artist I’ve come to see, however, is Tetsuya Otani, whose work departs so thoroughly from the Shigaraki style as to seem from another world. Otani’s hand-thrown porcelain chases the precision of machine manufacture. Its skin is smooth and naked, like that of a baby. I wanted to know why he was making such beautiful but plain stuff.
Right now, though, I have a few hours to kill, so I drive into the mountains to find the I.M. Pei-designed Miho Museum. The Miho is a kind of Japanese Getty, opened in 1997. It’s perched on a thick-forested mountain top like something a hermit might build if the hermit had several hundred million dollars. To reach it you walk through a hill via a gleaming, curving science-fiction-y pedestrian tunnel and emerge on a bridge that’s supported by a harp-string array of steel cables. The Miho was commissioned by an industrial-fortune heiress who also made time to found a sect in the 1970s, variously described as an art-centric religion and a sinister cult.
As traveler’s luck would have it, the museum is showing an astounding collection of ceramics by the 18th-century artist Ogata Kenzan, whose name means “northwest mountains.” His painted cups, bowls, and trays leave the viewer giddy, so varied and playful are they in style and form.
At home with Momoko and Tetsuya Otani
Five or so kilometers from the Miho is the home that Tetsuya Otani shares with his wife Momoko—also a gifted ceramic artist—and their three girls and a dog. It’s beautiful, with farmhouse mud walls and high wood beams that employ traditional temple joinery. Everything on the main floor revolves around the kitchen, which is far larger than usual in a Japanese house, reflecting the Otanis’ passion for communal cooking and eating with friends, many of whom also make pottery. The shelves, in the dining area and kitchen, are filled with both Tetsuya’s and Momoko’s pieces.
The work of Tetsuya Otani
Lately attracting attention among collectors in Beijing, Shanghai, and Taiwan, Tetsuya shuns both wabi-sabi imperfection and Kenzan decorative exuberance. Everything he makes is to be used, mostly in the kitchen or at the table: tiny matcha urns with clinking lids, curved-belly flower vases, delicately spouted teapots, tiny soy dispensers, little round boxes. The pieces are finely lipped and polished to a supple smoothness; their creamy matte glaze begs to be caressed.
Tetsuya’s pottery has thrown off all temptation toward decoration. The potter’s goal, he says, is to remove as much information as possible from his ceramics, seeking pure functional forms, because “things that work give pleasure.”
"The potter’s goal, he says, is to remove as much information as possible from his ceramics, seeking pure functional forms, because 'things that work give pleasure.' ”
He studied in Kyoto, hoping to design cars, but when the economy skidded in the nineties, he shifted to graphics and ended up teaching product design (“how to make molds”) at the Ceramic Institute in Shigaraki, where he met Momoko and, on the side, learned throwing and glazing clay. By 2008, their house was built and he embarked on a ceramic career. He’s now in his late thirties.
I watch him work in the studio, which has wheels for him and Momoko, as he forms and pokes a bit of clay that will become a tiny strainer inside a teapot. A few feet away, a large machine mixes clay while sucking air from it, then extrudes large, irresistibly smooth noodles of the stuff. The machine is close to the same color as the clay. Tetsuya grins and admits he had it custom-painted to obliterate the standard industrial green. A clue to his fastidious brain.
The pure cup and the pure bowl
Later, we sit at the long kitchen table and look at bowls and cups and teapots and plates and discuss this idea of removing information from one’s work.
“The pure cup,” Tetsuya says, through Momoko’s translating, “and the pure bowl: They can accept anything, become a vessel for anything. Cultural information is eliminated. And then the cup or bowl can be applied to any culture.”
“The pure cup and the pure bowl: They can accept anything, become a vessel for anything. Cultural information is eliminated. And then the cup or bowl can be applied to any culture.”
One may begin with the form of a traditional Japanese offering bowl. Decorative motifs are removed until it approaches neutrality. Eventually you “come down to the point where we can use it on our table, not for the gods’ offerings.”
Momoko adds: “Tetsuya strips the bowl of the divine.” He produces smooth dinner plates as blank canvasses for food—altars, really. They’re used in fancy Osaka and Kyoto restaurants to showcase chef art. His works are unsigned, unmarked.
“Tetsuya strips the bowl of the divine.”
But cultural negation negates a specific culture, and Tetsuya says he has lately realized, when showing his works in China, that they are in some way indelibly, irreducibly Japanese. “I now feel that,” he says, “but I don’t have the answer yet about why I feel that way.”
The potter approaches, but never finds, ideal functionality. Tetsuya tweaks the ancient teacup form a wee bit from batch to batch, always seeking the right feel of cup in hand, the right curve of handle against thumb and finger. This lonely, incremental search for ideal form, endlessly repeated, is itself very Japanese.
The motivation is pleasure, however, not denial. Tetsuya and Momoko are exuberant foodies, and have found that their table-centric philosophy resonates globally through their gorgeous Instagram feeds, @otntty and @otnmmk, with more than 20,000 followers between the two for their pictures of utensils and food.
Tetsuya is also funny. He calls the clay mixing machine Mr. Hiroshira, “my only employee.” What about the beautiful industrial kiln in the next room, I ask? “No,” he says, “I work for it.”
Return to Kyoto
A few nights later, in Kyoto, my wife and I visit a little chocolatier and bakery called Assemblages Kakimoto, near the Imperial Palace. In the minimalist showroom up front I buy a box of orange biscuits enrobed in dark chocolate, each biscuit not much bigger than a postage stamp. Beyond the front space is a narrow, pretty room with a half-dozen seats or so against a counter, facing a tiny kitchen. We order chocolates and cakes and glasses of thirty-year-old palo cortado sherry. Two women to our right—the only other customers in the café—have come for the chef’s omakase dinner. With each course they look gobsmacked, enraptured by the treats placed in front of them. It’s beautiful food, for that is the Kyoto style. Each composition sits on the pale canvass of an Otani plate.
The entanglement of much fuss and no fuss that lies at the heart of many things Japanese is hard to describe, but when I palm one of the Otani pieces that we brought back from Japan, it seems to embody that contradiction. My favorite is a little round vase, the size of a tennis ball, whose satin smooth sides curve up to a sharp-lipped hole that’s big enough to accommodate the stem of a single bud. In weight and delicacy and touch and every other aspect the vase seems, to me, as close to perfect as it can get. It holds a lot of information about Japan. △
Editor's Choice: Journey to Japan
The Beauty of Use
Hidden in the Japan Alps, a Czech-born artist makes woodstoves that match the simplicity of Japanese interiors. Read more »
The Skyward House
Japanese architect Kazuhiko Kishimoto designs a human-scale house for a retired teacher. Read more »
Repair With Gold
The Japanese tradition of wabi-sabi. Read more »
A Platform for Living
A weekend refuge in Japan’s Chichibu mountain range consists of a simple larch wood structure and two North Face tents for bedrooms. Read more »
Zen and the Art of Knife-Making
Using skills derived from the ancient craft of samurai sword-making, a blacksmith in the Japan Alps makes knives so delicate and dangerous they turn chopping into an artful act of passion. Read more »
In Search of Tenkara
The founder of Tenkara USA travels to Japan and brings back the traditional method of fly-fishing with a long rod and without a reel. Read more » △
Zen and the Art of Knife-Making
Using skills derived from the ancient craft of samurai sword-making, a blacksmith in the Japan Alps makes knives so delicate and dangerous they turn chopping into an artful act of passion.
A blacksmith in the mountains of Japan uses skills derived from the ancient craft of samurai sword- making to forge knives from a steel that is considered the finest base material of the knife-making art.
Cutting, slicing, mincing, dicing, boning, peeling: Over time, these mundane jobs have become, for me, the most satisfying tasks in the kitchen. Now, I experience knife-work as a meditation on all that will unfold after food leaves the chopping block. With each cut, I’m trying to shape ingredients to their ideal form, whether it’s a fine mince of onion designed to melt in a pan as a base for a sauce or fifty wedges of apple that need to keep succulence while retaining their shape in an autumn pie. The key to this repetitive-motion, Zenish state is a sublime knife: balanced in the hand, dangerous, delicate, an obedient lover and assassin.
I found my sublime knife after a lot of looking. It has a blade of Aogami Super carbon steel and was hand forged in a mountain town called Niimi, 150 kilometers (93 miles) northeast of Hiroshima, at the shop of a fifty-seven-year-old blacksmith named Shosui Takeda.
My Takeda
If you lay my Takeda 180-millimeter Super Sasanoha Gyutou chef’s knife beside my shiny stainless Shuns and Globals and Henckels, it looks weathered, almost preindustrial. The thin blade has a mottled black finish called kurouchi. The blade tapers sweetly to a gunmetal gray edge whose sharpness approaches that of a razor. You can see the resin used to affix the tang as it was slid into a hole in the Indian rosewood handle during construction. The handle is octagonal, to answer the shape of enfolding fingers and palm. Near the upper rear of the blade’s spine, roughly stamped into the metal, are Japanese characters, plus a heart and the Western letters AS. The characters mean “Niimi. Shosui. Aogami Super.” The heart is something Takeda-san’s blacksmith father started to put on his blades many years ago. Takeda-san says he has never been quite sure what the heart means.
Finding the perfect blade
I have not been to Niimi. I met my Takeda—and, later, two more of them—through Google’s search power and the matchmaking tastes of an American in Tokyo named Jeremy Watson. Watson is a thirty-nine-year-old American of UK and Hong Kong ancestry who moved to Tokyo after a period teaching English in Japan (where he met his wife) and a period learning about, and selling, Japanese knives in Manhattan. In 2012, he founded Chuboknives.com, selling products he found by scouting artisan blacksmiths around Japan. Initially, he hand-wrapped each order, inserting a thank-you note into slim boxes covered in Japa- nese stamps, and sent them on their way to Australia, Europe, and the UK, where chefs and foodies were beginning to notice his trade in rare beauty. Now his business is such that he has automated the shipping. But the boxes remain lovely and intricate, befitting jewelry, and to receive a Takeda in the mail feels like a gift, even if you’ve paid for it.
“We wanted to be a small family business that was connecting small-scale artisans to chefs and home cooks,” Watson says. Big Japanese knife-makers, like Shun and Global, were taking up more and more display space in stores like Williams-Sonoma (where once German companies like Henckels had ruled), but “I realized that the smaller artisans and blacksmiths were really underrepresented. Shibata, Takeda, or Tanaka—the craftsman that we’re currently working with—weren’t really out there.”
The absence of these knives from the major retailers can be explained by the minuscule production of operations such as Takeda Hamono, as the company is called.
Takeda's workshop
“There are three blacksmiths, including me, at the shop,” says Shosui Takeda (whose answers were translated for me by Watson). “We spend eight hours a day forging, twenty-five days a month. In total, we produce 250 knives a month. If we calculate the number of hours all of us work, essentially each person is producing about three knives per day.”
The quality of a handmade knife derives from the strange mutability of steel when it’s repeatedly heated and hammered to alter its molecular structure. The blacksmith, using skills derived from the ancient craft of samurai sword-making, is always chasing an ideal: a blade strong yet somewhat exible, thin but not brittle, able to take an edge and hold it for a long time. A molecular map of a knife would reveal a variety of attributes across its form, determined by cycles of quenching (to harden the steel) and tempering (to selectively soften it). The spine may be softer than the edge. The steel that Takeda uses, Aogami Super (AS), is considered the finest base material of the knife-making art, but it’s also known to be temperamental in the forge, and few blacksmiths bother with it. Takeda has been using AS for twenty-five years, after discovering it in a steel-maker’s catalogue, and after realizing that customers would pay a premium for the uncanny thinness and edge retention that AS offers. “As far as what I’ve seen,” Watson says, “I don’t think anyone makes knives as well as he does.”
“As far as what I’ve seen, I don’t think anyone makes knives as well as [Shosui Takeda] does.”
"The steel that Takeda uses, Aogami Super (AS), is considered the finest base material of the knife-making art, but it’s also known to be temperamental in the forge, and few blacksmiths bother with it."
Watch the YouTube videos of Japanese knife-makers at work: heating steel and iron to narrow temperature tolerances in coal-fired furnaces, then beating away at the metals—using both power hammers and tools wielded by hand—until they begin to fuse and morph like slow-motion Plasticine. The shape of the knife is judged by eye—as is the temperature of the hot steel, judged by the color of its glow in the fire. Heat, hammer, cool, and repeat. Sparks fly. The blades curl out of shape, then return to form under the blacksmith’s art. I’ve never seen anything so beautiful and fine that is produced by such fierce whacking and grinding.
"I’ve never seen anything so beautiful and fine that is produced by such fierce whacking and grinding."
That said, Takeda’s approach benefits from modern insights. “I’ve learned a great deal by collaborating with the steel-makers. Through trial and error and using high-resolution microscope photography to see how the steel looks after it’s forged, I’ve been able to eliminate problems with the forging processes.” He quenches his blades in successive baths of hot oil, whose temperature is closely regulated, then sharpens the edge with wheels and stones of increasingly fine grit. His wife and two daughters fix the tangs in the handles at the end, and handle other shop duties.
Dangerous business
The work looks dangerous because it is: “When we’re working in the summer with short sleeves,” Takeda says, “we get burns on our hands and arms every day. This is just part of the job and no big deal.
“What’s more serious are the repetitive strain injuries to my back, shoulder, elbow, and knees. Eight years ago, I had back surgery, and earlier this year, I had surgery on my right knee. I’m currently doing monthly injections so I can keep working. My grip strength is also significantly weaker than it used to be.
“The most serious is the hearing and vision damage. I use earplugs, but I still have hearing damage. Also, constantly looking at the coal-burning oven while forging has damaged my sight.”
"When we’re working in the summer with short sleeves, we get burns on our hands and arms everyday. This is just part of the job and no big deal."
All that pain may explain the paradox of the knife market in Japan. The rise of the global food and chef culture has created unprecedented demand for fine knives, and Watson says artisan shops have more orders than they can fill. The Internet makes new connections between cooks and artisans possible. It would seem to be a perfect time to grow a blacksmith’s business.
“The American solution to this would be to hire more people and build a larger facility,” Watson notes, “but that’s not necessarily the mentality here. A blacksmith team consists of three or four people, and it takes years to train.” Nor are young Japanese lining up for the work. This does not surprise Takeda. He did not intend to be a blacksmith himself; he helped around his father’s shop for bowling money, and didn’t take up the work properly until he was twenty-eight. Were his father not in the trade, he would never have pursued it.
Takeda describes the paradox this way: The knife business is good, the forging business is not.
“During my father’s time,” Takeda says, “there were forty-seven blacksmiths in Niimi—most making agricultural implements [as Takeda’s shop still does]. Now, there are just a handful. The small knife-forging business is literally going extinct. There are very few blacksmiths left.”
Care and maintenance
In my knife drawer are Japanese stones that I use to keep my Takeda knives sharp. The stones, soaked in water, give up a creamy slurry as the carbon steel of the knife is drawn across it. When the knives are done, I use a special little stone to smooth the water stones for the next session. Sharpening is a calming ritual that with a little practice leads to a gleaming thin line of razor sharpness along the gray edge of the blade.
When the knives are sharp, and again after every use, I carefully dry them, because Aogami Super is extremely prone to oxidation. It rusts in minutes. The rust is removed with a light scrub, should I fail to completely dry the knife; this is another little ritual that I enjoy. Takeda is now making an AS line with stainless cladding, which he calls NAS, to prevent rust, but I shall stay old school on further orders as long as he continues to produce them. And there will be further orders, even though his knives run from $120 for a beautiful little paring knife called a “petty” to $380 for an absurdly long, wondrously light Kiritsuke slicing knife that is my favorite cooking tool in the world.
Takeda’s blades have a gentle fifty-fifty bevel, meaning that each side of the blade tapers equally to the cutting edge. This is easier to sharpen for an amateur than the single-side bevels common on many Japanese knives. Beveling and blade shape, like everything else to do with Japanese knives, are complex and relate to the food to be cut: vegetables versus meat versus fish. Some blades are designed for species of fish, others according to what the fish is going to be used for. Everything is about form: of the blade, of the food.
These sublime blades support a Japanese kitchen culture of sublime knife-work, precise almost beyond belief. One gets a glimpse of it at a very good sushi bar, while a multicourse kaiseki meal in Kyoto is like a doctoral dissertation.
"These sublime blades support a Japanese kitchen culture of sublime knife-work, precise almost beyond belief."
Wielding my Takedas, I know that I shall never have such skills. But I do have knives that allow me to meditate on the ideal every day. △
The Tree-Hugging Woodworker
A portrait of California furniture-maker Sean Woolsey
Sean Woolsey loves trees. He celebrates the perfect imperfection of the trees' inner beauty by making wood furniture by hand in California.
Woolsey, now in his early thirties, has always made things. From sewing clothes to building skateboard ramps to baking bread. In 2010, he began making furniture, out of curiosity more than anything else. He deconstructed old furniture to learn how things are made. The first real piece of furniture he built himself was a writing desk for his then-girlfriend. She liked the gift, evidently. She married him.
Woolsey’s work and life is strongly influenced by the Japanese philosophy of wabi-sabi, which recognizes the beauty of imperfection as imprint of time. To the wood artist, wabi-sabi is embodied in the naturalness of the uneven, asymetrical touches to remind us of our own and the trees' perfect imperfections. In contrast to mass-producing furniture, which can take away these imperfections, Woolsey chooses to show the truth and rawness of wood, worked by hand.
The California native, who admits to obsessing over the quality of every piece that leaves his atelier, has always been captivated by the beauty of nature’s artistry and gains inspiration from the grandeur of a mature tree and the elegance contained in its wood. In his work, he has stayed true to the same simple ideal over the years: He designs and makes things he wants in his own home. And today, that's the place the entrepreneur shares with his wife, Sara, in Costa Mesa, California.
We caught up with the designer, furniture-maker, and fine artist only a short time after the birth of his daughter, Ondine, to talk about what home means to him, what traditions make his his modern products timeless, what inspires his designs, and more.
A conversation with Sean Woolsey
Who are you, in a nutshell?
A husband, father, artist, woodworker, tinkerer, artist, businessman, creative, friend, surfer, ping pong enthusiast, amateur knife-maker, bread-maker, pizza-creator, dreamer, risk-taker, traveler, tree-lover, ever curious human.
How did you grow curious about designing and making furniture?
It started very naturally and slowly. I was burnt out on making clothing and running my own clothing line. I was drawn to creating things with my own hands and to being more connected with what I was making, instead of just designing it and having someone else make it. I have a real obsession with creating, whether it be a pizza oven in my yard, furniture, a knife, or my own house.
"I have a real obsession with creating, whether it be a pizza oven in my yard, furniture, a knife, or my own house."
What inspires your designs?
So many things and people, but mostly the inspiration is rooted in making furniture that I would like in my own house and like to own for years, not just what is on trend. Much of the inspiration comes from the act of designing and tinkering around. Designs evolve, ideas feed other ideas, and things move with movement.
"Designs evolve, ideas feed other ideas, and things move with movement."
Your modern products appear rooted in tradition. What timeless merit drives your practice?
Functionality, with an utter respect and appreciation of materials and craft.
Is there a continuous theme to your designs?
I don't think so. I think, the only theme is making the best quality products that we can. The theme of materials and design is always changing and progressing.
How do you choose and source your materials?
The wood we use is predominantly American hardwood, such as walnut, white oak, or maple. We purchase most of it locally and occasionally purchase directly from mills, usually on the East Coast. We feel honored to work with wood, and we love trees. We plant a tree for every piece of wood furniture we sell, in honor of the customer, in partnership with the Arbor Day Foundation. It is our way of giving back to nature what it has loaned to us. We also work with steel, brass, glass, leather, et cetera. And we are always looking for new and fun ways to incorporate mixed materials and creating a story with the materials. We are fortunate to have many other talented crafts people locally, who help us with these other materials.
"We feel honored to work with wood, and we love trees."
What makes you a modernist?
The way of thinking about clean, good design that is functional, beautiful, and accessible — and designing to that.
What does quiet design mean to you?
Quiet design to me means designing slowly and enjoying the process. I often enjoy the process more than the end result, as many artists would.
"Quiet design to me means designing slowly and enjoying the process."
Talk about the immensely beautiful fine art pieces in your Copper Series and their synergy with your furniture-making.
The art is a release for me. It always has been. It is the complete opposite of furniture-making, which is very accurate, wrong or right, and precise. The artwork on copper is fluid, free-flowing, expressive, and experimental. Mistakes often make it better or more interesting. The Copper Series was inspired by the ocean, and its meaning to me. The series is ongoing and ever-evolving but always the same size and always inspired by the ocean, whether it be the color, movements, or captivating calm or power it holds.
Describe your dream home...
A home that is comfortable, in a beautiful location in the mountains or desert, with treasures that we have collected all over the world, and open to sharing meals with friends and family.
What does “home” mean to you?
A refuge where we can relax, recharge, make memories, share stories, laugh, cry, and feel good about it all.
What’s your favorite place in the world?
Oh, so many. I have been fortunate to travel a lot internationally. I am really drawn to Japan, and their culture and way of life. To me, Japan is simple, humble in its design yet meticulously thought out, timeless in its approach to craft. And the Japanese are the most focused people I have ever met. The mixture of it all is super intoxicating and inspiring.
What’s most important to you in life?
God. My family. Friends. Creative pursuits. Having fun.
Who is your design icon?
There are so many. The short list is Wharton Esherick, Dieter Rams, Robert Rauscheberg, Lloyd Kahn, Sunray Kelly, Jay Nelson, and Jean Prouve.
Who inspires you to be the person you are?
My wife and my friends largely inspire me to be who I am. As iron sharpens iron, they are constantly encouraging me, whether they know it or not.
What is your life philosophy?
This quote by Mark Twain sums up a lot of my life approach: "Twenty years from now you will be more disappointed by the things that you didn’t do than by the ones you did do. So throw off the bowlines. Sail away from the safe harbor. Catch the trade winds in your sails. Explore. Dream. Discover."
What are you working on these days?
We are constantly working on new designs; right now, some chairs. I am also working on some copper art, as well as a new art series that is going to be really fun. Also, we just had a beautiful baby girl three weeks ago, so... working on that right now (laughs). △
More of Sean Woolsey's work...
The Beauty of Use
Hidden in the Japan Alps, a Czech-born artist makes woodstoves that match the simplicity ofJapanese interiors.
Secluded in the Japanese Alps, a Czech oven-maker and his Japanese artist wife find creativity in daily life as she weaves rugs from goat hair and he smiths minimalist woodstoves that are as much modern steel sculptures as they are functioning furnaces.
“In November, the mountain puts on her autumn kimono, and it is lovely around a burning stove...”
The first time I saw one of Jirka Wein’s stoves, I was visiting friends in Matsumoto, a city in the valley that stretches along the eastern flank of the Japan Alps a few hours west of Tokyo. It was March, and I had arrived from California braced for the icy floors and bone-chilling drafts typical of Japanese houses built in the traditional style, which is to say without insulation or central heating. Instead, I stepped into a deliciously warm and cozy enclave. There in the entryway sat a fat black stove unlike any I had seen before. Woodstoves are not unusual in heavily forested rural Japan—I had owned one myself when I lived there, as had a number of my more rustic friends—but this one was glossy and sleek, stripped of any frill that might obstruct its absolute simplicity. It looked as much like a sculpture as a functioning furnace. A lively fire flickered against the round glass door, and above that, behind a second door, a pan of pasta baked in a brick-lined oven.
"It looked as much like a sculpture as a functioning furnace."
My friends were quite taken with their stove. It was like a pet, they told me, or a fifth family member with a knack for bringing together visitors and residents alike in toasty communion. Its origin was equally interesting: It came from a remote valley in the mountains south of Matsumoto where Jirka Wein, a seventy-three-year-old Prague-born artist, shaped steel while his wife, Etsuko Seki, wove rugs from goat hair. My friends had driven out to pick up their new acquisition and ended up staying to talk about poetry and pottery and wine—all, of course, while gathered around the inviting flames of a woodstove.
Visiting the oven-maker
I was so intrigued by this story that on returning home I called Wein to ask if I could visit the next time I was in Japan. He agreed, and six months later I found myself sitting beside him as he drove east toward his house from the small train station where I’d arrived. By then it was early November. It had rained the previous night, and as we climbed into the hills, the damp tree trunks stood out like black fault lines against the brilliant foliage. Wein, a grandfatherly man in suspenders and a plaid shirt, seemed as overwhelmed by the beauty of the landscape as I was. “We see the color descending from the top of the mountain, and one day it swallows the place where we are,” he said. His parents had been avid mountaineers, he told me, and the family spent summers in the mountains of Bohemia, instilling in him a lifelong love for alpine wilderness.
A life journey from Bohemia to the Japan Alps
His path from those mountains to these was far from direct. Wein grew up in the suburbs of Prague and studied stage design there before moving to southern France to pursue a master’s degree in art history and archaeology. By the time he graduated in 1973, the political situation in Soviet-occupied Czechoslovakia had made returning home impossible. He spent the subsequent decade as a wandering scholar, artist, and spiritual seeker. At a Gandhian ashram in India he learned to spin, and in Santa Cruz, California, he taught weaving. By the early 1980s, he was living at a commune in New Mexico. It was there that he met the itinerant poet and environmentalist Nanao Sakaki, who eventually led him to Japan.
“Nanao was living up in the mountains in an abandoned bear den, writing a play,” Wein recounted as he turned onto a narrower branch of the winding road. “He would come down to the commune to restock. We’d spend all night drinking and singing, and then he would go back up the mountain.” The two became friends and eventually traveled the western United States together, staying with the likes of Allen Ginsberg and Gary Snyder. When Sakaki returned to Japan, he wrote to Wein, inviting him to follow. “So I came. It was winter. Then spring came and the mountain was so beautiful I couldn’t believe it,” he said. Thirty years later, he hadn’t left.
At home with Seki
Wein rounded a final curve and pulled up in front of a large old-fashioned house hemmed in by wooded slopes. It was a perfect mild morning, the sky clear, the smell of smoke mixing with the sunlight. From somewhere far below, I could hear an invisible creek rushing past. Wein led me inside a cavernous entryway. The 140-year-old house had belonged to a powerful landowning family, he explained, but by the time he and Seki arrived with their daughter in the mid-1990s, it had been abandoned for decades. A flood had washed away all of the other homes in the hamlet, leaving only monkeys, deer, and wild boar for neighbors. Now, restored, the house was spare and majestic, composed of age-darkened wood and dusty plaster pierced by shafts of light. Gazing out at the wall of trees that pressed in from every window, I asked him if he ever tired of the mountain. “No, never,” he replied, deep smile lines radiating from the corners of his eyes. “I hope it doesn’t get tired of me.”
In the kitchen, Seki, a small, reserved woman in indigo farmer’s pantaloons and a blocky top, was arranging slices of cheese and tomato on top of pizza dough for our lunch. She nodded hello, then carried the pan over to the large stove in the center of the room, opened a side door, and slid it in. Wein donned a pair of black-rimmed glasses and joined her beside the stove.
“You see these two holes on the top?” he asked, pointing to pipes embedded on either side of the chimney. “These suck in warm air from above so that it creates turbulence.” He struck a wooden match and held it above one of the holes; the flame was instantly pulled straight down by the draft. He walked around to the front and told me to look in through the glass window. Behind the crackling flames, I could just glimpse rows of yellow firebricks similar to those used in ceramic kilns. “Wood flames at 600 degrees Celsius. Firebricks accumulate heat, and after they reach 600 it’s hard for things not to burn,” Wein explained. Together with the air system, the brick lining ensures that his striking stoves burn well, which is why they are as popular with his elderly neighbors as they are with design-conscious urban architects.
Wein has been refining this design nearly as long as he has been in Japan. Not long after he accepted Sakaki’s invitation to cross the Pacific, he met Seki, who at the time was weaving rugs in Tokyo (she has exhibited them nationwide). The pair soon moved to a small village not far from their current home. They grew most of their own food and made what they could by hand, learning from their self-sufficient neighbors. “We wove rugs and grew wheat and rye, and when we wanted to make bread, I thought about making a stove,” Wein said.
“We wove rugs and grew wheat and rye, and when we wanted to make bread, I thought about making a stove.”
He found himself fascinated by both the engineering challenges and the aesthetic ones. Older stoves were made of cast-iron parts assembled with screws. Newer ones had heat-resistant sealing materials between the parts and other additions such as catalytic converters that needed periodic maintenance. Wein imagined something completely different. “I wanted to make one without many technical tricks, that was simple, efficient—and for me this is very important—it had to be beautiful and fit well with the simplicity of Japanese interiors,” he said.
“It had to be beautiful and fit well with the simplicity of Japanese interiors.”
His solution was to weld rolled steel into simple forms assembled with the absolute minimum of fixtures (rolled-steel stoves are now available from many companies in Europe and the United States). The steel sheets are made by compressing hot metal between rollers and cooling it in an oil bath, which produces a rust-resistant surface that does not require paint. Since there are no small passages to become blocked by soot, his stoves can burn soft woods such as cedar that are plentiful in Japan. They are also durable and easy to maintain. He patterns their forms on the asymmetries of the natural world, because “if they were perfect circles or rectangles, you would get tired of them.” Each model is named after a plant or animal: peach, wolf, acorn, Japanese plum.
At first Wein did nearly all of the manufacturing himself while continuing to weave alongside Seki. By the early 2000s, however, he was making stoves full time in order to meet demand. Today he splits production between his home and several small family-owned factories in the prefecture: One laser-cuts the steel based on his designs, another rolls it, and a third handles the welding, with his help. The wooden handles come from a craftsman in the Tohoku region of northern Honshu. Wein cuts the firebricks and finishes the stoves himself, at the rate of about one per week, in an open workspace tucked against a lush hillside behind his house. He told me he likes this division of labor.
“When I’m here, I’m like a wild monkey. When I go there [to the welding factory], a bell rings at 10:00 and it’s teatime,” he said, settling into a bench beside the large slab of wood that serves as a kitchen table. Seki opened the door on the side of the stove and pulled out the pizza, releasing a gust of garlic and seared dough into the warm kitchen. She set the pan on the table next to a large bowl of salad greens and sat down across from Wein. As we ate, she talked about her work as a weaver, and I realized that although she is the quieter of the two, her clarity and strength of vision easily match his.
“We make functional things. When people use them, they create the beauty. In Japanese we say yo-no-bi,” she told me. Wein nodded: The expression, which literally means “the beauty of use,” is essential to him as well. It describes the tracks of rust that bloom from scratches on his stoves, the resonance of her earth-toned rugs against the wooden floors, the way their handmade dishes come to life when piled with food.
“We make functional things. When people use them, they create the beauty.”
“Daily life is quite a creative thing,” Seki continued. “Beauty is very important for our heart and spirit, so how we live is important. When I was thirty-nine, I came to live in the mountains. At first I was so shocked. It was too different, and Jirka was quite strict.” He interrupted: “In the beginning I didn’t want to have a fridge, because when you have one you don’t eat fresh things.” Seki continued. “Those ten years made me very strong, and they changed me. After ten years, nature became very close. Lately, Jirka goes to sleep early, and I’m up late. I hear deer crying, and I feel like we belong to the same community of living things in nature. I feel deep joy.”
Lunch had ended, and our conversation was winding down. “Jirka, should we make coffee?” Seki asked. “I’ll grind some,” he replied. They moved together to the kitchen counter, where Wein pulled out a hand grinder. Seki filled a pot with water and placed it on top of the woodstove. Imperceptibly, the beauty of use settled another layer onto its smooth black surface. △
Repair With Gold
The Japanese tradition of wabi-sabi
The Japanese savoir vivre has a name, yet is almost impossible to define. What does it feel like? Does it live in old objects or is it intangible? Wabi-sabi is the mindful balance between treasuring simply beautiful things and relishing freedom from things. When a piece of pottery breaks in Japan, the traditional practice is to fuse the pieces back together with gold lacquer. The Japanese word for this practice—kintsukuroi—doesn’t just refer to the method of repair, it also suggests that the tea bowl is more beautiful because of the crack. The gold is a bright line of the pottery’s imperfection. In the West, we tend to judge a repair by whether it is noticeable—the less evidence of a rip, scratch, or stain, the better. The traditional Japanese practice is the opposite. In a Japanese tea ceremony, guests are served with the most cracked and different side of the tea bowl facing toward them. The imperfections are emphasized and appreciated.
The sense that imperfection makes the tea bowl more beautiful, or at least more interesting, is known as “wabi-sabi.” Wabi-sabi is very difficult to define. Considered by many to be the aesthetic of Japan, it is a know-it-when-you-see-it kind of thing. And like most aesthetics, wabi-sabi is about more than how things look. It suggests a way to live.
“Things wabi-sabi are appreciated only during direct contact and use; they are never locked away in a museum. Things wabi-sabi have no need for the reassurance of status or the validation of market culture.” — Leonard Koren, author of Wabi-Sabi for Artists, Designers, Poets, and Philosophers
I missed breakfast the morning of my first tea ceremony. Only four months into my stay in Japan, I had not yet adjusted to the Japanese concept of time. When my friend said she’d pick me up at seven, she meant six forty-five: a fifteen-minute sign of respect.
My stomach growled as we drove along the Sai River toward downtown Kanazawa. Japan’s famous cherry blossoms had just reached this small city nestled between the Japanese Alps and the Sea of Japan, on their bloom north from Okinawa to Hokkaido.
To celebrate the season, the small treats, wagashi, served with tea at our ceremony that morning were pink cherry-blossom-flavored macaroonesque pastries. Unfortunately for my empty stomach, we were each given a single, tiny wagashi before our tea was served. Everyone fell silent as they focused fully on eating their treat. A tea ceremony is a cross between performance art and meditation. Each action is intentional and slow; it is a kind of spiritual exercise. The simple act of making and then drinking tea is elevated through total attention to the people and objects involved.
Once we finished our wagashi, an elderly tea master served us ceramic tea bowls full of frothy matcha that required two hands to hold. Splotches of green and black interspersed with faint gold lines covered the surface of each bowl. The rim was uneven, and small nicks lined the bottom. The tea master showed us how to examine our bowl before our first sip. This amounted to a lesson in applied wabi-sabi. We paused to find and create beauty from the simple, humble, and nonobvious—the cracks in our ceramic tea bowls. Cultivating a wabi-sabi mindset requires overriding our default responses to what qualifies as beautiful and what qualifies as ugly, what is worth paying attention to, and what is not. A tea ceremony is one way to practice this, and it is equally important (and useful) in day-to-day life.
Transforming the ordinary
For me, the most important moment of the morning happened once the tea ceremony concluded. We were directed into a drafty back room and told to wait there for lunch. A few minutes later, a teenage boy showed up and placed a stack of seven bento boxes on a table near the door. We passed the boxes around and then began to eat, still wearing the kimonos we had put on for the ceremony, seated atop overturned foam seafood crates.
One of the many sections of the bento box held kaki no ha zushi, a specialty of Kanazawa’s prefecture. Kaki no ha zushi is a square of rice topped with thin slices of fish or vegetables and then wrapped in a persimmon leaf. I eagerly tore open my leaf as I would the paper wrapping of a burger, ready to finally fill my stomach. Seated right beside me was a sixteen-year-old girl named Sui who had taken me under her wing during the ceremony. When one of the tea masters said something my limited Japanese could not decode, she would discreetly slip her iPhone from the sleeve of her kimono and type into a translator. “When you have to stir the tea, more calm”... “Bow before the step back”... I read on a screen the girl shyly turned towards me.
Sui eyed the crumpled leaf of my kaki no ha zushi with concern. Then she reached over, took it from my hands, and folded the leaf neatly around the rice, gently smoothing each corner down with her fingertips so that it matched her own. She handed it back to me, and I felt moved.
Feelings and folding
“It’s a feeling.” That’s as close as I have come to a definition of wabi-sabi from a Japanese person. It came from a thirty-something man named Kei, whom I worked beside as a line cook in a kitchen in Niseko. At the time, I had just been trying to make conversation while we chopped daikon. I didn’t know quite what he meant. “It’s a feeling.”
But months after Kei’s definition, and weeks after the tea ceremony, I kept thinking about Sui’s simple action: folding my leaf. And each time I did, I felt a particular way. I started to understand what Kei meant when he told me that wabi-sabi is a feeling.
It’s the feeling you get when you look at an old kitchen table, not the feeling you get when you look at pristine china in a cabinet. It’s a strange mix of nostalgia for an object’s past and gratitude for its present functionality—and something else, harder to define. It’s the feeling you get when you see a dead flower, or the last traces of a sunset. It is a recognition of the cycles of life and death, use and disuse. It is the feeling you get when you see the natural world reflected in material objects—a rusty patch of metal, a worn piece of wood. Asymmetry is the toll the elements take.
"Asymmetry is the toll the elements take."
Wabi-sabi is looking at the imperfections of the world and transforming them into a kind of beauty—not by changing them, but by changing how we relate to them. Instead of trying to get away from boredom, endings, and loneliness, the feeling of wabi-sabi is what happens when you work to make those things beautiful. It is the philosophical analog of the gold line to emphasize the pottery’s crack.
The leaf that Sui folded for me was nothing if not impermanent—I’d be throwing it away in mere minutes. It was an everyday object—just a little leaf around my lunch. And nothing about our surroundings suggested that the lunch was important—we were in a tiny little room, not even sitting at real tables. But Sui slowed me down, she recognized that the leaf and moment, while imperfect, were still a site of possible beauty. She was not trying to make a point. The ceremony was over. She was just living. And that is what wabi-sabi is: the beauty of the everyday, the small, the inconspicuous. The beauty of life as it is lived.△