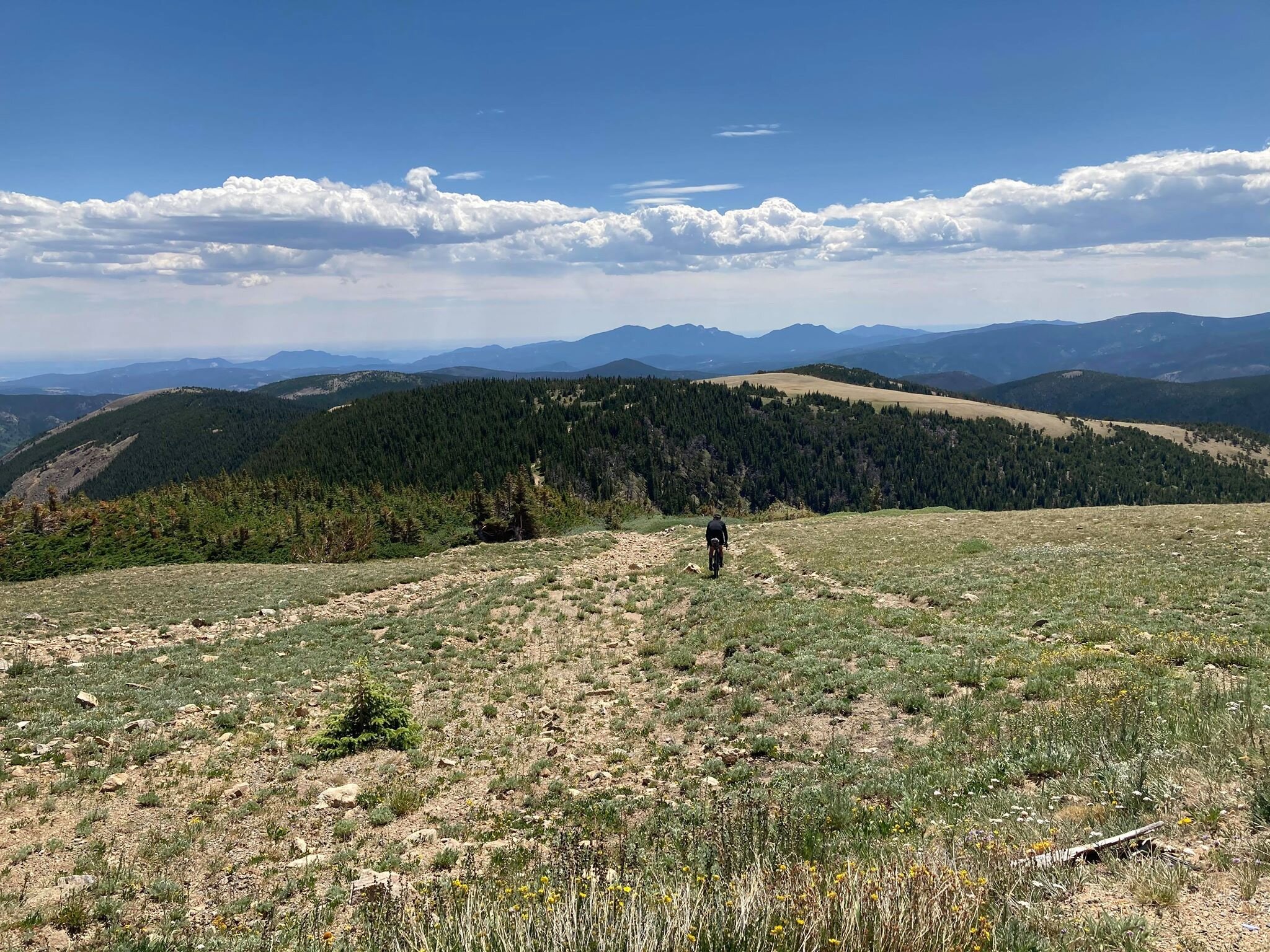
Inspirations
Explore the elevated life in the mountains. This content debuted in 2015 with Alpine Modern’s printed quarterly magazine project.
Makers on Board
Born out of passion for the ride, handcrafted snowboards, splitboards, and skis by Vancouver Island's Kindred Snowboards feature marquetry artwork.
Kindred Snowboards was born out of passion for the ride and the opportunity to grab a snowboard press off Craigslist. Meet the spirited couple who handcrafts custom snowboards, splitboards, and skis featuring marquetry artwork on Vancouver Island.
Evan Fair and Angie Farquharson have been designing and making custom snowboards and skis together in their backyard woodshop on Vancouver Island since 2010. We squeeze in a weekend visit just before the busy winter season to get a glimpse into their craft, their art, and their humble lifestyle in a rural community on the island’s east side. The couple built the Kindred Snowboards brand from scratch. They cultivated the low-impact operation out of nothing more than a passion for the ride and the desire to make a higher-quality product—yet without any background in fabrication.
Beautiful Comox Valley and Mount Washington straddle this area fifteen miles (twenty-four kilometers) north of Courtenay, British Columbia, where their home and shop are located. Weather on the east side of the island is mild and temperate year-round, a surprise given the substantial annual snowfall in the nearby mountains. The couple’s home sits at sea level in a forest, the mountains hidden from view. Land plots are large here, spreading neighbors apart. Industry in this area is a miscellany, though mostly milling timber and small-batch farming. Neighborhood homesteading makes the community largely self-sufficient—the local crops and dairy products go directly to the local population.
Pressed to jump
“How is a snowboard made?” the couple, both in their late twenties, asked each other one day before it all began. Not long after they pondered the process it may take to create the boards their life revolves around, a snowboard press came for sale on Craigslist. Fair and Farquharson, as adventurous as they are curious, grasped the opportunity. At the time, they were living out of a camper van and chasing the best snow to ride. But they made the purchase, hoping the investment would be the impetus to launch them into a more serious endeavor.
They were committed. Being avid riders themselves, they knew exactly what they wanted in a board, what their ideal board would look like, feel like. So they learned and improved upon the techniques to make a better product. Their goal was to create high-performance boards and skis that enhance, not hamper, the user’s skill, style, and fun on the snow.
“Some experienced riders know exactly what they want, down to the numbers,” Farquharson says. With others, the Canadian gear artisans spend significant time getting to know the customer’s riding style and preferences. “For the topsheet artwork the questions are a bit more ephemeral,” she says. People have asked for anything from the silhouettes of their favorite mountain to portraits of their pets or pop-culture idol, and even memorials to lost loved ones. Kindred’s Limited Edition Series, on the other hand, features artwork infused with an alpine or coastal sensibility. “I draw from my own personal experiences in nature, as it is common ground for people who spend their recreation time outdoors,” Farquharson says.
“For most people the way their gear looks is a very close second to how it rides,” she knows from experience. “People who go for a custom build impact the end product directly, which can be empowering. The ride becomes a distilled reflection of the rider and what they want out of their alpine experiences. In the end, Evan and I hope our work inspires people to be themselves and to be better riders.”
“People who go for a custom build impact the end product directly, which can be empowering.”
Shop talk
That mission to make a superior board hasn’t shifted or been compromised in the five years since Kindred began. Each board is treated with the same intense amount of care and precision. Personal connection with each customer and hands-on craftsmanship that goes into every board leave the couple remembering almost every individual product. The number of orders Kindred fulfills has been growing every year. By the end of this season, they are projecting to have made approximately 150 boards, splits, and skis.
Their search for the right place for Kindred led the couple to a tree-lined rural spot with a woodshop, old smokehouse, and former boathouse turned into a woodshed. They purchased the property with the intent to grow their business and live in the same place. “At first, we considered commercial property around the area, but it made more sense to have a shop very close to home,” says Fair. “The former owner was a cabinetmaker, so the shop already existed and was set up for woodworking.”
"Personal connection with each customer and hands-on craftsmanship with every board they make leave Fair and Farquharson remembering almost every individual product."
Sunlight filters into the shop through the grapevines that walk along the top of the awnings and the edge of the roof. As the gentle breeze blows, the leaves dance in the wind, making the patches of light dance on the floor. The view from the workshop doors is still lush and green this time of year; an occasional chicken races by or stops to graze for bugs in the grass. Inside, the walls are neatly laced with deliberately arranged hand tools and jars of screws and nails hanging from lids nailed to the shelves, organized according to the makers’ workflow. Fair’s homemade shelves display boards and skis in progress. It’s obvious the two designed this workshop with careful thought.
Fair puts on an album by Little Feat as the machines are slowly starting up. All of us pull on protective face masks before he begins sanding the core of a board he prepped the night before.
Meanwhile, at the giant table in the back of the shop, Farquharson sets up the topsheet, the piece that is most visibly “Kindred” to those familiar with the distinctive snowboards. The topsheet, a thin wood veneer, is intricately designed. The decorative patterns and graphics are meticulously cut from different woods and inlaid using a technique called marquetry. Defined by the grain and color of the woods, the outline of a fir tree begins to show light and definition in its branches, and a moon shows its craters. This detailed, time-intensive process makes Kindred boards one-of-a-kind art pieces.
Farquharson cuts the wood with her penknife. We talk about Kindred’s customer base as she carves out a moon from a delicate sheet of gorgeous black walnut.
“We’ve had incredibly strong local support from shops and individuals, but we are fortunate to ship all around the world,” she says. “We even had a Japanese fellow arrive unannounced from the other side of the world who had planned his whole vacation around watching our build process...He is now a friend of ours.”
Return to the Valley
Fair sets up a bottom sheet to be cut with a drag knife mounted to a CNC machine (computer numerical control machine, or automated milling machine used to make industrial components). He tinkers with the calibration on a laptop next to it. Satisfied, he hits “start” and the knife begins to cut out the Kindred logo from the sheet. When I ask him about their initial business ideas and how things have developed through the years, he pauses. “Humble beginnings for sure,” he replies.
“The concept was founded while we were living in a truck and camper. We had left the island to travel throughout Alberta and BC looking for the next ski resort. When we decided to embark upon the snowboard-building adventure, we returned to the Comox Valley, where we already had a network of support. We initially saw a potential niche in building high-quality North American skis and snowboards, and quality and beauty remain central to every step of the process—no cutting corners.”
A complex custom build can take the two up to thirty work hours to design and build a board or a pair of skis, not counting drying and curing time. The Limited Edition Series builds, where Kindred makes a small number of products with similar designs, still take up to fifteen hours each.
The day goes by quickly, and before we know it, the afternoon sun starts to set. The board is ready for the nal press, and all the layers are assembled with a chemical-free epoxy slathered on between each layer as the machine applies a healthy dose of heat and pressure. It’s fascinating to watch the steel tube stock apply pressure, making the epoxy ooze out the sides, slowly creating mountains on the floor. The snowboard press that started the whole operation is beautiful in its frugality—a testament to Kindred’s mindset.
"We initially saw a potential niche in building high-quality North American skis and snowboards, and quality and beauty remain central to every step of the process—no cutting corners.”
Community board
A couple of miles from the workshop, a local mill saws logs into lumber for the core pieces, the main foundation and center of each board, sandwiched between layers of fiberglass and carbon fiber. Farquharson and Fair know the owners of the mill well, and the family’s son is out working when we visit. With a population this small there is a strong reliance on others and an understanding that you are a connected member of the island community. Your actions greatly impact the local environment and its residents. Thus, good relationships with neighbors are important for businesses like Kindred to thrive.
As we observe the milling, Fair steps in to help move the last few logs on the run. “Many people are here for recreation—not specifically to ski or snowboard—they come to enjoy a work-life balance and the mild climate, fostering a slower pace overall,” he tells us.
What’s in a name?
How did the name “Kindred” originate? “We wanted to recognize how constantly blown away we are by the support of our community, friends, and family,” says Farquharson. “On another level, we give homage to the incredible relationships that are forged through alpine winter sports and lifestyle. Nothing quite compares to charging through fresh snow engulfed by the euphoric hoots and hollers of your friends. Those snowy moments, when we’re living a shared experience, feel like pure magic. When you are surrounded by people who embody that joy on and off the snow, you can’t help but feel like family. Those are our people. Kindred felt genuine and accessible, as we were sure that other skiers and snowboarders could relate.” △
Architecture, Made On Site
The husband-and-wife founders of Scott and Scott Architects design-built their own off-grid cabin with the adventurous spirit of the powder boarders they both are.
Built by husband-and-wife architects for themselves, an off-grid cabin in the mountains of Vancouver Island captures the adventure and freedom of powder boarding, free of rigid ideas.
David and Susan Scott wanted to make architecture. But not in the way one imagines married architects making architecture for themselves — drawings of their dream mountain retreat, years in the drawer, just waiting for the right building site. No. Building their own alpine cabin, the Vancouver-based architects wanted to design and build in a singular act.
In 2006, a longtime friend led them to a piece of land he’d come upon when planting trees at 4,265 feet (1,300 m) above sea level, on the northern end of Vancouver Island in British Columbia, Canada. “We had never been on the snow in the area until acquiring the building site,” says David Scott, speaking for the adventurous couple. “We fell in love with it at first sight, and the people and terrain are really special.” With almost 50 feet (15 m) of annual snow accumulation, the remote community-operated alpine recreation area of Cain is known for legendary powder.
At the time, the couple, who met in architecture school in Halifax, Nova Scotia, worked for established firms and spent long hours in offices, drawing. “We have a love for building and being outdoors,” says Scott, who appreciates drawing as an important part of design. Now building their own off-grid cabin, however, they wanted to channel the freedom they feel when powder boarding into an immediate design process centered in adventure and not heavily in rigid plans. “We began the project with a desire to work with a greater level of freedom, where the specifics of the site and available materials would inform the work in a direct and unfiltered manner.”
Scott and his wife knew they had a narrow window in life, before having children, to complete construction on their own on long weekends and holidays, and with help from friends.
“We began the project with a desire to work with a greater level of freedom, where the specifics of the site and available materials would inform the work in a direct and unfiltered manner.”
Hand in hand: Design and construction
Inspired by the materials available around the site and the environmental conditions, construction was planned to avoid machine excavation, to withstand the very deep annual snowfall, and to resist dominant winds. Accordingly, the structure was elevated above the height of the accumulated snow on the ground. “The use of full-length, unsawn logs provided us with the ability to get height in a manner that used the wood’s strength the same way Douglas fir spar poles are used as sail masts,” Scott explains.
The cabin, primarily constructed from Douglas fir, gets more refined from the outside in. The columns are unworked logs, the beams and joists are rough, bandsaw-milled, and the walls, floors, and ceilings are clad in planed boards. The cabinetry is made from construction-grade fir plywood. The exterior is clad in cedar that has weathered to the tone of the surrounding forest. Both woods are harvested in the area.
The roof form began with a simple gable, rotated to direct the snow off the back of the cabin. A half-dormer was then introduced over the entrance to direct snow away from it, funneling the snow into the prevailing winds.
Family life at the cabin
Today, childhood memories are already being made at the cabin. The Scott family now includes two young daughters, who Scott says are both on skis and love the snow.
Much of the approximate 1,075-square-foot (100-sq-m) cabin’s interior is designed and made by Scott and his wife. The main living space is small, and the family spends much of the time on the long, cushioned bench eating, playing games, and relaxing from a day on the snow. “Our favorite spot is by the large window,” says Scott. “Both for the ever-changing view of the forest, but also in appreciation of the effort that went into its installation.” He drove the glass overnight on a rented flatbed and hand-positioned it with a group of friends the next day — “an incredibly smooth effort, given its size and weight.”
The remote site is directly accessible by gravel road five months of the year. During the other months, equipment and materials are brought up by toboggan. There is no electricity, and a wood stove provides the heat. Water is collected from a local source and carried in. The Scott family cherishes the simple lifestyle the mountain hideaway affords. “We enjoy the solitude of not having cell phones and gadgets around to distract us,” says the architect, who finds “a wonderful freedom” in seeing no bars of coverage on his phone. “This is an incredible place for our daughters to love being in the mountains as much as we do.”
“This is an incredible place for our daughters to love being in the mountains as much as we do.”
The powder hounds come up here as many weekends as possible during the winter, but they also love the warmer temperatures in spring when snow is still plentiful. “It’s incredibly peaceful,” Scott says. “The fall is fantastic when the blueberries are ripe, and we try to spend Thanksgivings on the mountain, splitting wood and enjoying dinners with friends.”
Adventure by design
The off-grid cabin was David and Susan Scott’s foundation project and formative in their desire to start their own architecture practice, Scott and Scott Architects, with the goal of spending more time in the mountains. To both, making architecture on site is ultimately the most direct, enjoyable way of working, and one that provides the greatest opportunity to understand materials and detail resolution and evolution. Today, the firm is working on projects in Whistler and Squamish, and in their province’s interior high country. “We love working in these challenging locations where adventure is the reward,” says Scott.
(Alpine Modern has covered the A-frame cabin Scott and Scott built in Whistler for a young family of skiers and snowboarders.)
What’s Inside?
Architect David Scott opens the door to the off-grid snowboard cabin he built with his wife on Vancouver Island to show his three most treasured artifacts hidden inside.
The cast-iron pot
“We have a Björn Dahlström-designed cast-iron pot we slow-cook many meals in on the wood stove, which is essential to how we live when we are [at the cabin].”
Get your own: Björn Dahlström designs pots and casseroles for the Finnish company Iittala. Dahlström’s current line is stainless steel, but cast-iron pots and Dutch ovens similar to the one in the picture are available from brands like Le Creuset, Sur La Table, and Lodge.
The splitting maul
“I have a love for Swedish axes. Of my collection of over 100, the most used and loved is the Gränsfors Bruk splitting maul, which powers through the yellow cedar rounds. It is a beautiful object from a company we greatly admire. Whenever cutting wood, I look at the stamped initials of the smith that made it, with appreciation for his work and respect for a very old company which values and celebrates the workmanship of the individuals within it.”
The Gränsfors Bruk splitting maul’s head is heavier than the head of splitting axes, and the poll is designed for pounding on a splitting wedge.
The blanket
“We love our Hudson’s Bay blanket, which was a wedding gift from the architect I worked for for a number of years, before we began our own practice. I’ve often thought that a Bay blanket should never be bought for oneself and is something that carries meaning as a gift.”
Buy it for someone: Woolrich offers Hudson’s Bay Point Blankets under the offcial license of the historic Hudson’s Bay Company. The legendary blankets have kept generations of trappers, hunters, fur traders, and Native Americans warm and comfortable. 100-percent wool, loomed in England. △